Situation
References orders
Wholesale
- 500 emails per day pure incoming orders
- 8-person sales team
- Manual entry in ERP system
- Processing time per order approx. 7.5 minutes
Challenge: Enable for attractive, higher-value tasks, high fluctuation
Lösung
paipz® module orders
- Automated recording of the required data with paipz®
- Reduction in processing time per order to around 2 minutes
- Additional quality assurance
- Peaks can be handled without any problems
- Higher employee satisfaction and lower staff turnover
- More dedicated sales tasks can be taken on
Industry
Wholesale
Document Type
Orders
Result
98% degree of automation
70% shorter processing time
”The introduction of the paipz® platform was an important step for us. The collaboration with the Weyp team was very professional and transparent. What I particularly like is the flexibility of the software. We can easily adapt it to our individual requirements and always feel that we are in control. The results are impressive - more efficiency and less administrative work.
Head of Sales, 8-person sales team, 20.000 employees
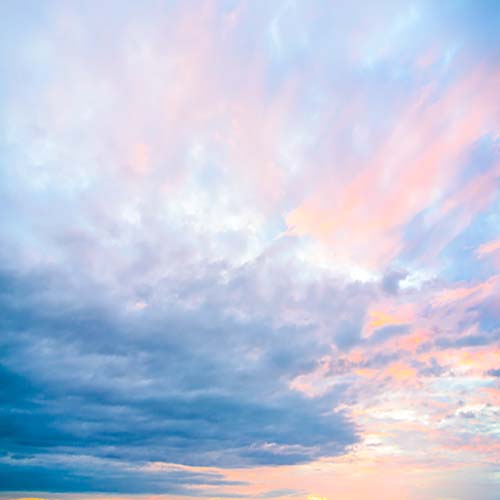
Orders
Orders are processed manually by employees:
Step 1:
Incoming emails – The process begins when orders are received by email. Employees must check each incoming email, identify the order and manually extract relevant information.
Step 2:
Manual data entry – Once the order has been identified, employees must manually enter the data into the ERP system. This step is error-prone and time-consuming as it requires accurate recording and transfer of information.
Step 3:
Review and approval – After data entry, orders must be manually reviewed and approved to ensure that all information is correct and complies with company policies.
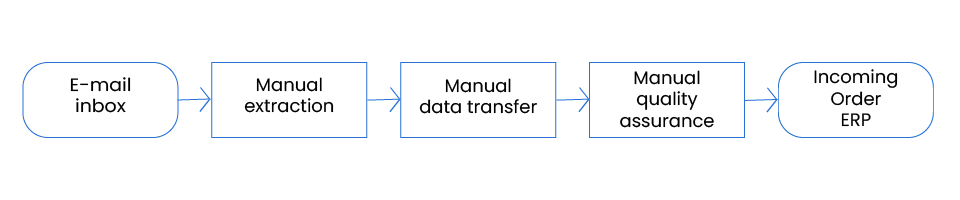
Fully automated process with AI
Step 1:
Incoming emails and data extraction – In the automated version, AI is used to analyse incoming emails and automatically extract relevant information. This is done with the help of AI-supported document understanding, which is used to understand the content of the emails and identify the required data.
Step 2:
Data integration into the ERP system – The extracted data is seamlessly integrated into the ERP system without manual intervention by employees. This not only reduces the susceptibility to errors, but also speeds up the entire process considerably.
Step 3:
Automatic checking and approval – Based on predefined rules and algorithms, the AI can automatically check and approve the orders. This minimises human error and shortens the processing time.
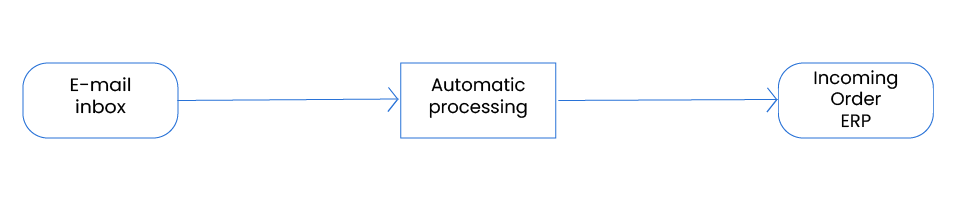
Partial automation practical example
Our practical example shows the benefits of partial automation. The process goes through further steps here.
Incoming emails are first classified according to whether it is an order. Any replies, enquiries or complaints also arrive in this email inbox. These must first be sorted out.
The data from the incoming emails is then enriched with additional data from the ERP before the employees carry out a check. The process is simplified in the following diagram:
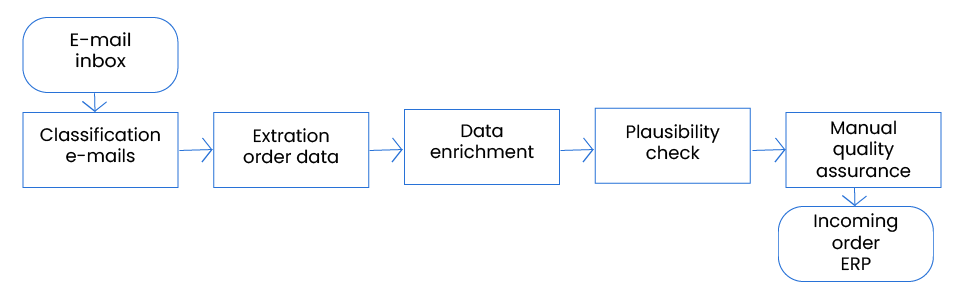
In this project, the task was to reduce the workload of an 8-person sales support team. An average of 500 emails were processed per day as pure incoming orders and manually transferred to an ERP system. The average processing time for an order was therefore around 7.5 minutes.
By reducing the workload, the team should finally be able to concentrate on ‘higher-value’ tasks. Staff turnover in the team was very high due to the very monotonous nature of the work and replacements were time-consuming due to the unattractive nature of the work.
With the help of the system outlined above, the average processing time could be reduced to less than 2 minutes, despite additional quality control. This corresponds to a reduction in workload of over 70%.